Zawory bezpieczeństwa muszą spełniać wymagania techniczne oraz warunki zabudowy i eksploatacji. Dobór zaworu zależy od parametrów urządzenia chronionego – ciśnienia, temperatury roboczej, rodzaju czynnika i wymaganej przepustowości. Istotne są także: minimalne i maksymalne ciśnienie, rodzaj sprężyny, rodzaj przyłącza oraz sposób uszczelnienia. Konieczne jest uwzględnienie warunków otoczenia, w jakim zawór będzie pracował.
Dobór dobrego zaworu bezpieczeństwa to ważny element projektowania instalacji przemysłowych, który wymaga szczegółowej analizy wielu parametrów technicznych i warunków pracy. Profesjonalny proces doboru musi uwzględniać podstawowe parametry ciśnieniowe, charakterystykę medium, warunki środowiskowe oraz specyfikę danej aplikacji. W praktyce inżynierskiej często spotyka się sytuacje, gdzie standardowe rozwiązania katalogowe nie spełniają wszystkich wymagań projektowych. Należy wtedy przeprowadzić pełną analizę, pilnującą takie czynniki jak: lepkość medium, temperatura pracy, obecność zanieczyszczeń czy ryzyko krystalizacji. Idąc dalej ważne jest wzięcie pod uwagę spraw związanych z przepustowością i charakterystyką przepływu.
W procesie doboru zaworów bezpieczeństwa podstawaową rolę odgrywa precyzyjne określenie warunków brzegowych i parametrów granicznych instalacji. Właściwa analiza powinna obejmować następujące aspekty techniczne:
- Maksymalne ciśnienie robocze systemu
- Przewidywane scenariusze awaryjne
- Wymagana wydajność upustowa
- Kompatybilność materiałowa
- Warunki montażu i konserwacji
Specyfika doboru zaworów do instalacji wysokociśnieniowych
Instalacje wysokociśnieniowe stawiają szczególne wymagania wobec używanych zabezpieczeń – przede wszystkim w kontekście charakterystyki dynamicznej zaworów bezpieczeństwa. Medium robocze może wykazywać nietypowe zachowania w warunkach przekroczenia parametrów krytycznych, co wymaga zastosowania specjalistycznych rozwiązań konstrukcyjnych (np. zawory z podwójnym gniazdem lub układy tandemowe). Należy także pamiętać o zjawisku histerezy ciśnieniowej oraz możliwości występowania kawitacji podczas zrzutu medium.
Aspekty eksploatacyjne i diagnostyczne
Aktualnie systemy przemysłowe wymagają niezawodnego działania zaworów bezpieczeństwa, możliwości ich diagnostyki i monitoringu. „Inteligentne zawory” wyposażone w czujniki położenia i systemy diagnostyczne są standardem w krytycznych aplikacjach. Jak zapewnić optymalną współpracę zaworu z systemem sterowania? Należy uwzględnić protokoły komunikacyjne i standardy przemysłowe stosowane w danym zakładzie. Prawidłowa integracja systemów bezpieczeństwa z infrastrukturą automatyki wymaga szczegółowej analizy interfejsów i protokołów komunikacyjnych:
Uwagę musimy zwrócić na dobór materiałów konstrukcyjnych – przede wszystkim w przypadku mediów agresywnych chemicznie lub mających substancje ścierne. Trwałość i niezawodność zaworu bezpieczeństwa w dużej mierze zależy od właściwego doboru materiałów uszczelnień i elementów roboczych. Czy zastosowane materiały będą odporne na korozję naprężeniową? Jakie będą skutki długotrwałego oddziaływania medium na elementy zaworu? Te pytania muszą zostać szczegółowo przeanalizowane na etapie projektowania.
Jak dobrać zawór bezpieczeństwa do instalacji przemysłowej i nie stracić głowy?
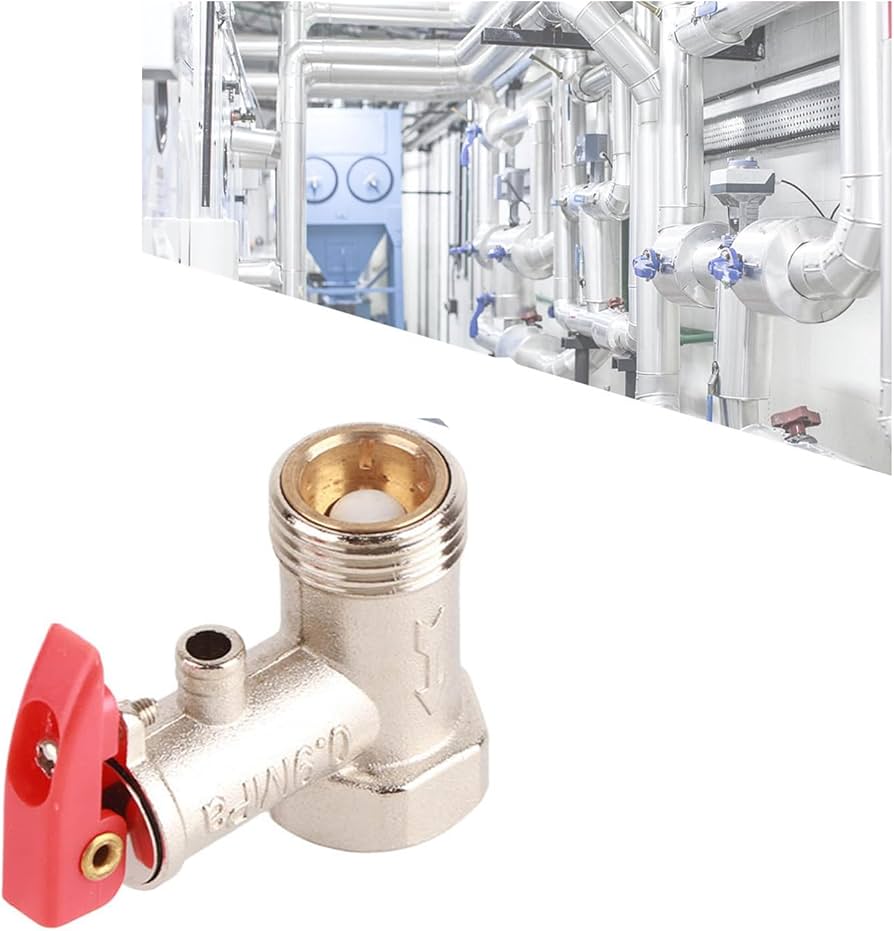
Pierwszym parametrem przy doborze zaworu bezpieczeństwa jest określenie maksymalnego ciśnienia roboczego instalacji. Należy uwzględnić charakterystykę medium, jego temperaturę oraz wymaganą przepustowość zaworu. Ciśnienie początku otwarcia zaworu powinno być wyższe od maksymalnego ciśnienia roboczego o wielkość pilnującą tolerancję wykonania oraz różnicę ciśnień wynikającą z oporów przepływu. Ważnym aspektem jest także materiał wykonania zaworu, który musi być odporny na działanie medium oraz warunki zewnętrzne.
W czasie wybierania zaworu bezpieczeństwa trzeba wziąć pod uwagę jego konstrukcję – może być sprężynowy, ciężarkowy lub sterowany pilotem. Zawory sprężynowe są najpopularniejsze ze względu na prostotę działania i relatywnie niskie koszty. Zawory ciężarkowe stosuje się głównie w instalacjach o niskim ciśnieniu, jednak pilotowe przy dużych przepływach i tam, gdzie wymagana jest wysoka precyzja działania. Należy także pamiętać o zgodności zaworu z odpowiednimi normami i dyrektywami, w szczególności z dyrektywą ciśnieniową PED. Wybranie dobrego zaworu powinien być potwierdzony obliczeniami pilnującymi wszystkie możliwe scenariusze awaryjne.
Multilayer Safeguards: Klucz do niezawodnej pracy systemów chłodniczych
Projektowanie zabezpieczeń nadmiarowych w systemach chłodniczych stanowi fundamentalny element zapewnienia ciągłości procesów przemysłowych i bezpieczeństwa instalacji. Redundancja zabezpieczeń gwarantuje stabilną pracę systemu nawet w przypadku awarii pojedynczych elementów. Implementacja wielopoziomowych systemów ochronnych obejmuje także rozwiązania mechanicznei elektroniczne systemy kontroli. Stosowanie podwójnych zaworów bezpieczeństwa, zdublowanych czujników temperatury oraz niezależnych systemów zasilania awaryjnego pozwala na minimalizację ryzyka wystąpienia poważnych awarii.
- Redundantne systemy zasilania
- Zdublowane czujniki ciśnienia
- Wielopoziomowe zabezpieczenia temperaturowe
- Automatyczne systemy bypass
- Niezależne układy alarmowe
- Zapasowe systemy sterowania
Aktualnie rozwiązania techniczne w zakresie redundancji wykorzystują zaawansowane algorytmy predykcyjne, które umożliwiają wczesne wykrywanie potencjalnych problemów. Systemy te są w stanie automatycznie przełączać się na zapasowe układy, zanim dojdzie do krytycznej awarii.
Inteligentne systemy zarządzania redundancją w instalacjach kriogenicznych
W spraw instalacji kriogenicznych ważne jest zastosowanie specjalistycznych rozwiązań redundantnych. Wykorzystanie zaawansowanych materiałów izolacyjnych oraz dedykowanych systemów monitoringu pozwala na utrzymanie stabilnych parametrów pracy nawet w ekstremalnych warunkach. Technologia ta znajduje zastosowanie w przemyśle kosmicznym oraz w zaawansowanych laboratoriach badawczych.
Membranowi strażnicy bezpieczeństwa – czyli kalibracja i atestowanie zaworów procesowych
Częste sprawdzanie i kalibracja zaworów membranowych ma podstawowe znaczenie dla bezpieczeństwa i efektywności procesów przemysłowych. Każdy zawór membranowy podlega ścisłym procedurom kontrolnym, które muszą być zgodne z normami branżowymi oraz wymaganiami prawnymi. Atestowanie obejmuje szereg testów, w tym próby szczelności, kontrolę poprawności działania mechanizmów zamykających oraz weryfikację parametrów pracy. Procedura kalibracji wymaga specjalistycznego sprzętu pomiarowego i doświadczonego personelu, który potrafi bardzo dokładnie ustawić punkty zadziałania zaworu.
W procesie atestacji uwagę zwraca się na stan membrany, która jest najbardziej narażonym na zużycie elementem. Certyfikowana kalibracja musi być wykonywana w regularnych odstępach czasu, zazwyczaj co 12 miesięcy, chyba że warunki pracy wymagają częstszych kontroli. Dokumentacja z przeprowadzonych testów stanowi ważny element w systemie zarządzania jakością zakładu przemysłowego.
Wyniki kalibracji są szczegółowo dokumentowane, a każdy zawór otrzymuje indywidualny certyfikat potwierdzający jego sprawność i zgodność z wymaganiami technicznymi. W kwestii wykrycia nieprawidłowości konieczna jest natychmiastowa wymiana wadliwych elementów lub całego zaworu. Przestrzeganie harmonogramu przeglądów i kalibracji mocno wpływa na niezawodność instalacji przemysłowych.